Toyota Boshoku
Toyota Boshoku, one of the world’s premium interior systems suppliers and filter manufacturers, develops and produces interior, filtration, and powertrain components. With world headquarters in Kariya City, Japan, Toyota Boshoku Corporation owns Toyota Boshoku America, Inc. (TBA) based in Erlanger, Kentucky. TBA and its affiliates, employ over 11,000 team members in 18 locations throughout the United States, Canada, Mexico, Brazil, and Argentina. TBA Group is a premier manufacturer of automotive interior systems, which include seat, door trim, headliner, substrate, and carpet in addition to air and oil filters for a variety of customers such as Toyota, BMW, and Subaru.
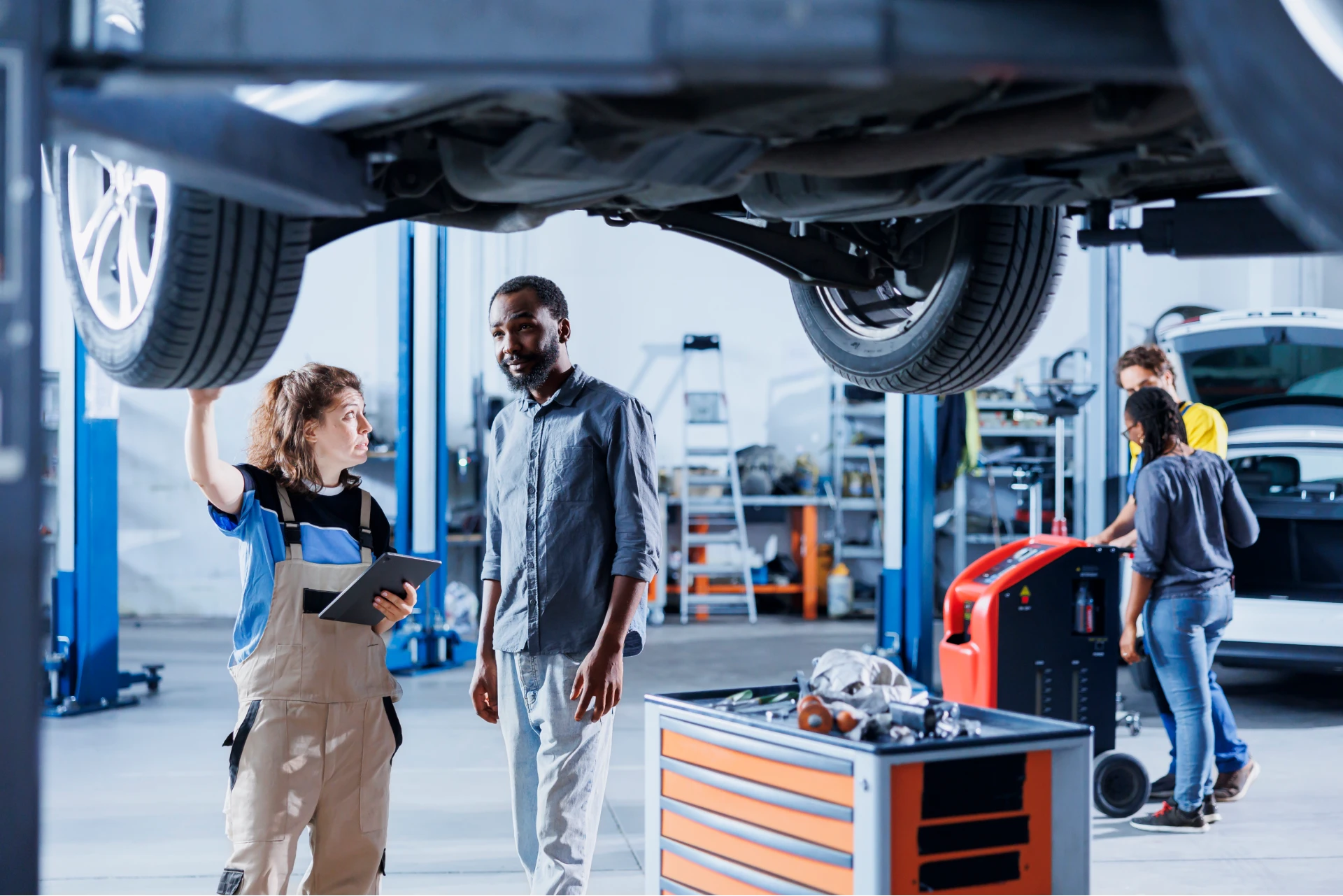
Toyota Boshoku faced challenges in manual material planning, inefficient production workflows, supply chain coordination issues, and inconsistent product quality. These inefficiencies resulted in delays, increased costs, and operational disruptions, prompting the need for improved processes and technological solutions to enhance performance.
Manual material planning
Manual material planning caused inefficiencies in just-in-time delivery, resulting in delays, inventory issues, and increased operational costs.
Complex purchase requisition
Overly complex purchase requisition process with excessive approvals caused delays and inefficiencies in procurement decisions.
Production order management
Inefficient production order management led to delays, affecting production timelines, resource allocation, and overall operational efficiency.
Production order management
Inefficient production order management led to delays, affecting production timelines, resource allocation, and overall operational efficiency.
To address the challenges Toyota Boshoku faced, advanced solutions were implemented to streamline operations and enhance efficiency. Automated material planning systems replaced manual processes, ensuring accurate inventory management and improving just-in-time delivery. The company adopted optimized production workflows, reducing lead times and enabling scalability. Real-time supply chain management tools were introduced to enhance coordination, reduce delays, and improve material flow. Additionally, automated quality control systems were implemented to maintain consistent product quality across all facilities. These technological advancements led to improved operational efficiency, cost reductions, and greater scalability to meet market demands.
- Material Resource Planning: Automated material planning enabled Toyota Boshoku to manage over 20 daily deliveries from a single supplier efficiently.
- Budgeting & Control A comprehensive budgeting tool was introduced, allowing department-wise budget creation and tracking actual expenditures against planned budgets.
- PR to PO Management: A streamlined workflow with defined departmental roles was implemented for purchase requisitions, integrating budget control to reduce approval bottlenecks.
- Digital Kanban: This ensured smooth production order management by visualizing workflows and reducing manual interventions.
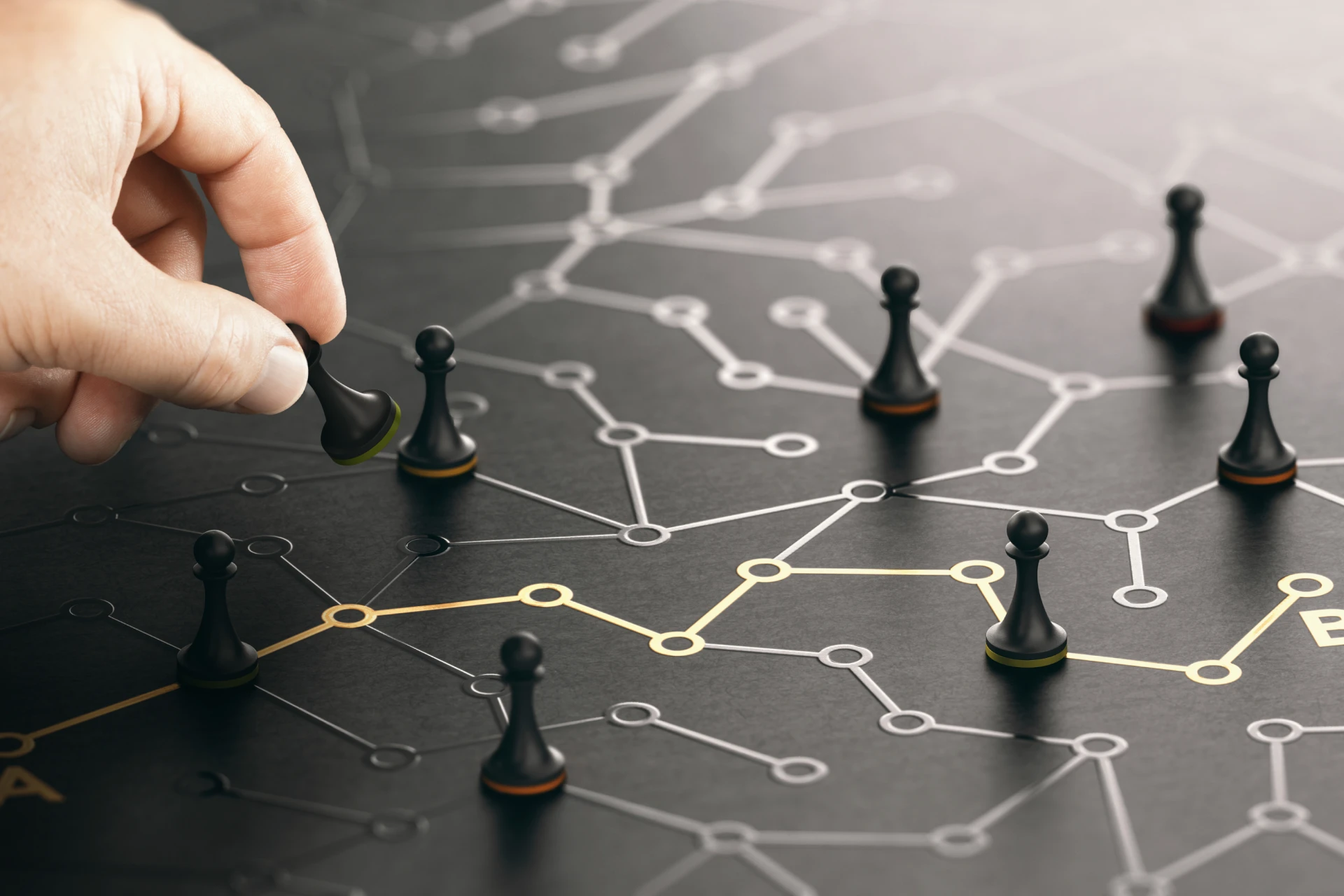
The implemented solutions improved operational efficiency, reduced lead times, optimized inventory management, enhanced supply chain coordination, ensured consistent product quality, and enabled scalable production, leading to cost savings and better market competitiveness.
Reduction in Lead Time:
Streamlined production workflows and automated material planning resulted in a 20% faster production cycle, meeting market demand more efficiently.
Cost Reduction:
Automation and integrated systems reduced operational costs by 15% through eliminating inefficiencies, minimizing manual errors, and boosting productivity.
Fewer Product Defects
Automated quality control systems reduced product defects by 25%, ensuring a higher level of product consistency and improving customer satisfaction.